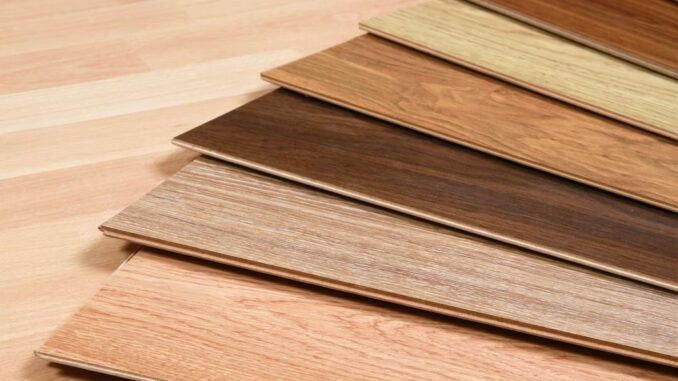
In the world of construction materials, few can match the durability, strength, and water resistance offered by marine grade plywood. Whether it’s used in boat building, creating docks, or constructing coastal homes, marine-grade plywood is specifically designed to withstand harsh marine environments. This article will explore the importance, composition, types, applications, and key characteristics of marine grade plywood, making it clear why it’s the material of choice for projects that require reliability in wet conditions. From its unique properties to practical applications, you’ll find all the information needed to choose the best marine grade plywood for your needs.
What is Marine Grade Plywood?
Plywood is a versatile material made by layering thin sheets of wood veneer and bonding them with adhesive. Regular plywood, often used in residential or light-duty applications, may not have the necessary durability or moisture resistance for projects exposed to water. Marine grade plywood, on the other hand, is specially designed for use in demanding environments like boats, docks, and coastal homes.
What makes marine grade plywood different is the way it’s constructed. The wood veneers are carefully selected for their durability, and the adhesive used is waterproof, ensuring the plywood doesn’t degrade when exposed to moisture over time. Regular plywood, though useful in many applications, simply cannot provide the same level of water resistance and longevity.
At its core, marine grade plywood is engineered to resist the elements — be it water, UV exposure, or physical wear. It’s specifically created to endure the challenging conditions found in the marine world, which is why it’s commonly used for boat hulls, docks, decking, and other structures constantly exposed to water.

Composition of Marine Grade Plywood
Core Materials
The core of marine grade plywood is typically made from layers of softwood or hardwood. The choice of materials is crucial in ensuring the strength and water resistance of the plywood. Softwoods, such as pine or spruce, offer lightweight durability, while hardwoods like mahogany or okoume provide higher strength and resistance to wear and tear. The key goal is to prevent the wood from absorbing water, which can lead to warping, swelling, or rotting.
In marine environments, wood exposed to water undergoes significant stress. The core material needs to be selected for its ability to resist moisture while maintaining structural integrity. Softwoods such as pine or spruce are chosen for their flexibility and strength under pressure, whereas hardwoods are valued for their resilience and long-lasting performance in high-moisture conditions.
Veneers
The veneers used for marine grade plywood are carefully selected for their smooth surface and strength. High-quality hardwood veneers such as okoume, mahogany, or birch are often used because of their excellent resistance to moisture and their aesthetically pleasing appearance. These top layers are glued together to form a smooth and robust surface, which is vital for both structural integrity and the application of varnishes or paint.
In particular, the veneers chosen for marine grade plywood are crafted to be free from defects. Imperfections like knots or voids can compromise the strength of the plywood and lead to premature failure, so only high-quality veneer is used. These layers are bonded with precision to create a surface that is as visually appealing as it is functional.
Adhesives
The adhesive used in marine grade plywood is what truly sets it apart from regular plywood. Typically, waterproof adhesives like phenolic or moisture-resistant (MR) adhesives are used to bond the veneers together. These adhesives prevent the plywood from delaminating under the stresses of water exposure, ensuring the plywood retains its strength and integrity even in wet environments. This resistance to water penetration is vital for projects exposed to constant moisture, such as boat building and dock construction.
In marine grade plywood, the adhesive isn’t just for bonding — it plays a crucial role in the longevity of the plywood. Ordinary plywood uses adhesives that are not designed to withstand water and high moisture conditions, which is why regular plywood can swell or fall apart when exposed to the elements. In contrast, the adhesives used in marine grade plywood are waterproof and resistant to breakdown, making the material highly durable even in environments that involve constant water exposure.
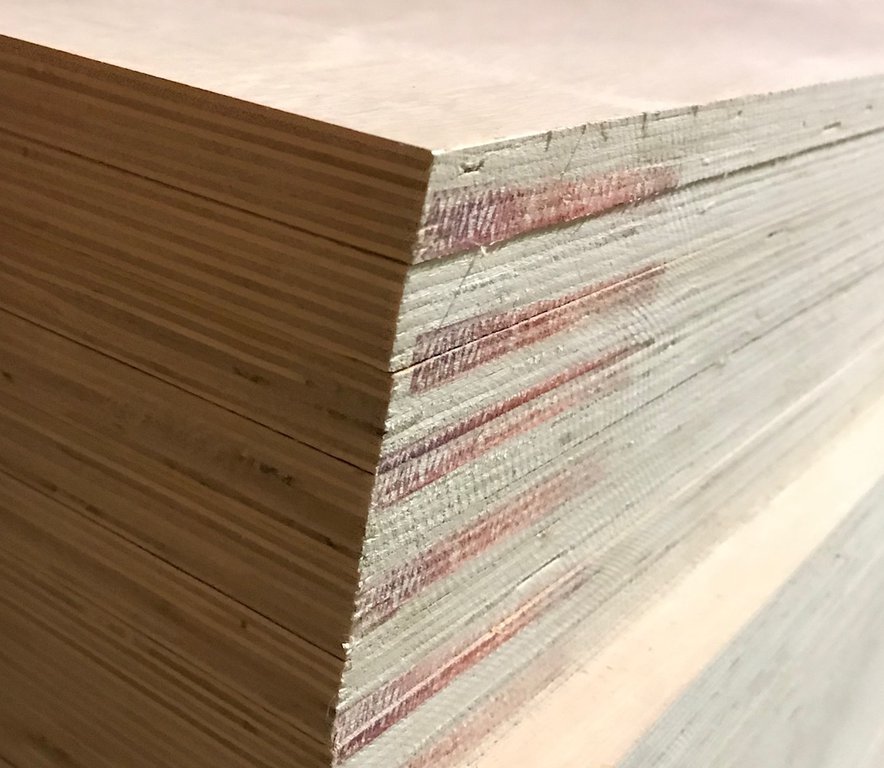
Key Characteristics of Marine Grade Plywood
Water Resistance
One of the defining characteristics of marine grade plywood is its exceptional water resistance. Regular plywood can absorb water, which leads to swelling, warping, and eventual decay. Marine grade plywood, however, is designed to resist water penetration, thanks to its high-quality adhesives and water-resistant veneers. This resistance makes it ideal for environments like boats, docks, and other applications where plywood is exposed to frequent or constant moisture.
In fact, marine grade plywood is often designed with a structure that resists the penetration of water through both its surface and edges. Its construction limits the risk of delamination (the separation of layers) even when exposed to water for long periods. As a result, it can endure much harsher conditions than regular plywood, which can swell, warp, or rot when exposed to water.
Durability
The durability of marine grade plywood is another key reason why it is the preferred material for boating and coastal applications. Its construction allows it to endure the physical stresses that come with marine environments. Whether it’s the forces exerted by waves on a boat, or the impact from heavy objects on a dock, marine grade plywood can handle it all without succumbing to damage. Additionally, its ability to resist wear and tear makes it suitable for long-term use in these challenging environments.
The tough construction of marine grade plywood helps it withstand mechanical stress, including impacts and vibration. This is particularly important in marine settings where materials are subjected to a combination of pressure, moisture, and physical forces that would break down other types of wood.
Strength
Marine-grade plywood is engineered to have a high strength-to-weight ratio, making it ideal for boat building and other marine applications. It can withstand the stresses of movement, impact, and load-bearing without sacrificing structural integrity. Whether used in hull construction or as part of the deck or framework of a boat, marine grade plywood provides strength and support while keeping the overall weight of the structure manageable.
The structural strength of marine grade plywood ensures that boats and other marine structures maintain their integrity, even under harsh operating conditions. The lightweight nature of the plywood also helps to keep the overall weight of a boat or dock down, which can improve performance and fuel efficiency.
Smooth Surface
The smooth surface of marine grade plywood is another desirable characteristic. It provides an excellent base for varnishing, painting, or fiberglassing. This smoothness ensures that the final finish of your project — be it a boat, dock, or outdoor structure — looks aesthetically pleasing and is protected from the elements.
When marine grade plywood is properly sanded, it can serve as a high-quality surface for applying coatings that will protect it from UV rays, moisture, and physical wear. The smooth surface also contributes to the overall quality and finish of the project, whether you’re finishing the exterior of a boat or preparing a surface for fiberglass bonding.
Resistance to UV Radiation
Marine grade plywood is often treated to withstand UV radiation. Continuous exposure to the sun’s rays can cause plywood to degrade, warp, or lose its structural integrity. Special treatments help marine grade plywood resist UV damage, ensuring its longevity in sunny, coastal environments.
UV radiation can cause wood to dry out and weaken, but with the proper treatment, marine grade plywood can endure this exposure without compromising its structural integrity. This feature makes it especially suitable for outdoor applications where sunlight is a constant factor, such as in boat building and deck construction.
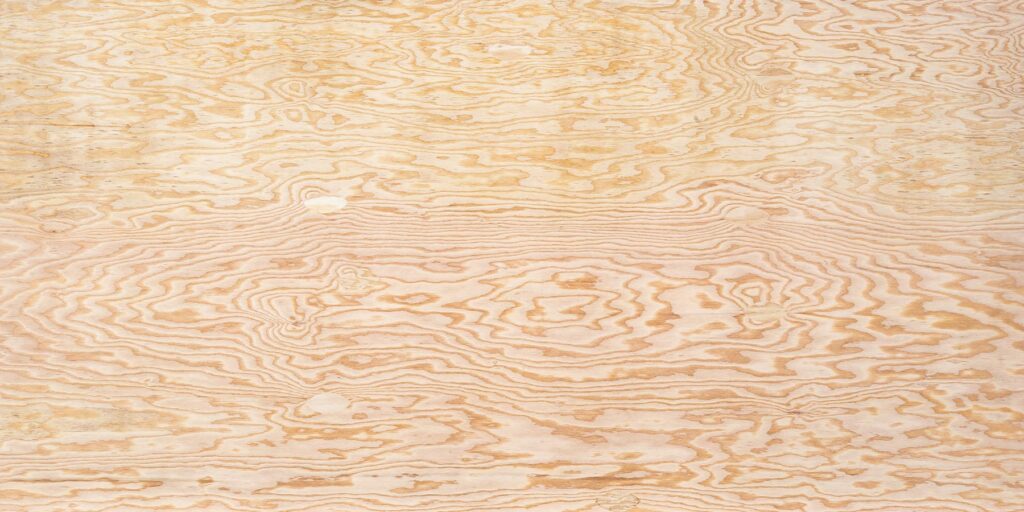
Types of Marine Grade Plywood
Okoume Marine Plywood
Okoume is a popular choice for boatbuilding due to its lightweight, strength, and ease of handling. This type of plywood offers excellent resistance to rot and moisture, making it well-suited for marine environments. Okoume marine plywood is favored for applications like boat hulls and decks because it combines strength with a relatively low weight, allowing for better performance and fuel efficiency in marine vessels.
Okoume plywood is commonly used in small and medium-sized boat construction due to its balance of weight and strength. This lightweight plywood is ideal for creating sleek, efficient boats that perform well on the water. Moreover, its resistance to rot ensures that boats built with this material will last for many years, even when exposed to harsh saltwater conditions.
Mahogany Marine Plywood
Known for its natural beauty and durability, mahogany marine plywood is another common choice for boatbuilding. Its deep, rich color and resistance to rot make it not only a functional material but an attractive one as well. It’s commonly used for both recreational and commercial vessels, providing strength and aesthetic appeal.
Mahogany marine plywood is often used in luxury boats and yachts, as its beauty adds an aesthetic appeal to the interior and exterior of a vessel. This type of plywood is durable enough to withstand exposure to water and sun, making it suitable for a variety of marine applications, from small dinghies to large ships.
Douglas Fir Marine Plywood
For larger vessels or structural applications, Douglas fir marine plywood is often the material of choice. This type of plywood is incredibly strong, making it ideal for building the main structural framework of a boat. Its resistance to moisture and decay ensures that it holds up under the demands of marine environments.
Douglas fir is well-suited for structural components, such as frames, bulkheads, and supports, in larger boats and ships. Its strength allows it to handle significant loads while still maintaining its integrity in high-moisture conditions.
Larch or Pine Marine Plywood
Both larch and pine have natural durability and resistance to decay, making them suitable for marine applications. These woods are often used in places where higher strength isn’t required but a reliable, weather-resistant plywood is necessary. Larch or pine marine plywood can be used for decking or other exterior applications exposed to water and the elements.
Larch and pine are often chosen for applications like boat decks or piers, where they provide reliable performance at a lower cost compared to more specialized materials like mahogany or okoume. These types of wood are durable enough to resist decay in marine environments, ensuring the longevity of structures like boat ramps and coastal walkways.
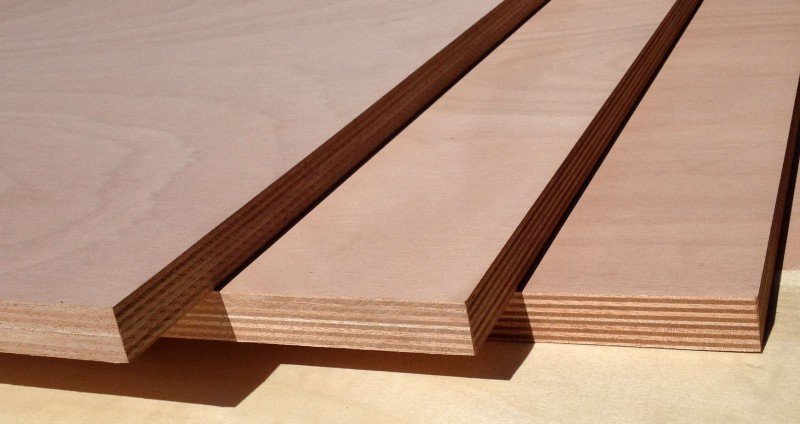
Marine Plywood Grades and Standards
BS 1088 Standard
The BS 1088 standard is widely recognized as the gold standard for marine grade plywood. Plywood that meets this standard must have no voids in the layers, waterproof adhesives, and high-quality veneers. This ensures that the plywood will perform well in marine environments, providing long-lasting durability and resistance to moisture.
Meeting the BS 1088 standard guarantees that the plywood is of the highest quality and able to withstand the challenging conditions of marine environments. This certification is highly sought after by professionals in the boating and marine industries, as it assures the plywood’s strength and water resistance.
Other Standards and Certifications
Other standards, such as those set by ASTM (American Society for Testing and Materials), also play a role in determining the quality of marine grade plywood. In addition to quality standards, certifications like FSC (Forest Stewardship Council) ensure that the plywood comes from sustainably managed forests, contributing to environmental sustainability.
FSC certification guarantees that the plywood is sourced from forests that are responsibly managed, helping to protect the environment while still providing a high-quality product. When purchasing marine grade plywood, it’s important to look for these certifications to ensure you’re getting a genuine, high-performance material.
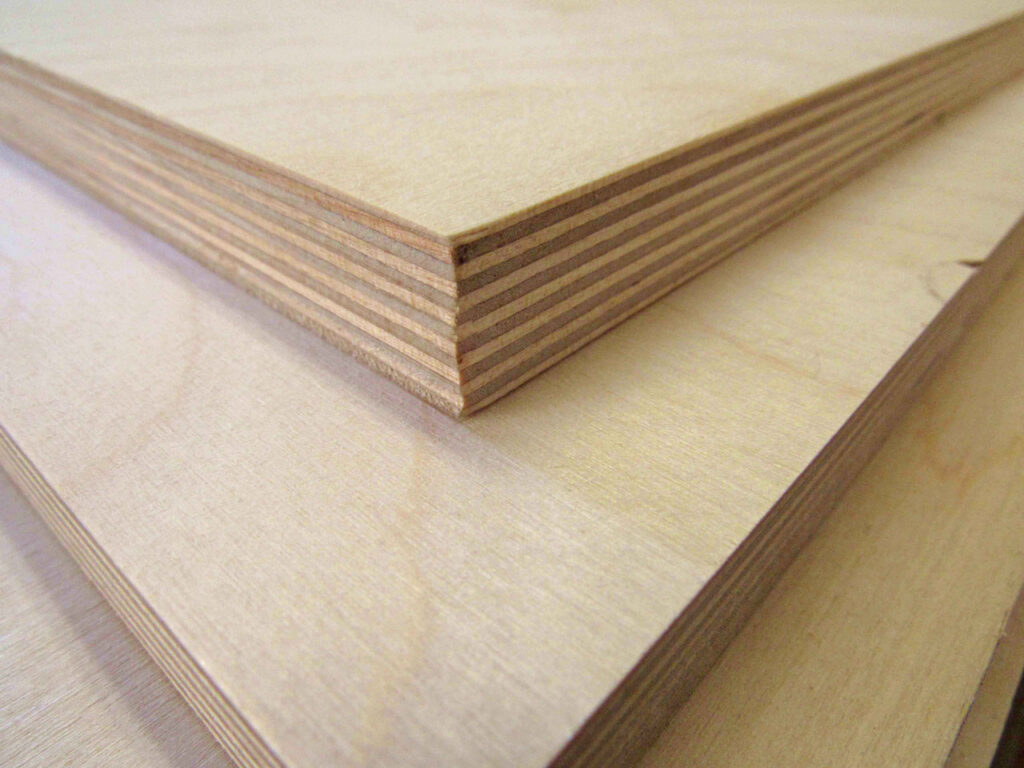
Applications of Marine Grade Plywood
Boat Building
The most common application for marine grade plywood is boatbuilding. It provides the necessary strength and water resistance needed to construct hulls, decks, and other critical parts of a boat. Marine grade plywood is preferred over solid wood or composite materials because it offers superior water resistance and strength at a lower weight.
Whether building small recreational boats or large commercial vessels, marine grade plywood is essential for ensuring the structure remains durable and resistant to water damage. Boats constructed with marine grade plywood can withstand the harsh conditions of the water without degrading, ensuring long-term functionality and performance.
Docks and Decks
Constructing docks, piers, or decks exposed to constant water contact requires a material that can withstand the elements. Marine grade plywood provides the perfect solution due to its resistance to rot and moisture. Its ability to handle the physical demands of outdoor use while maintaining structural integrity makes it ideal for these applications.
The strong, durable nature of marine grade plywood makes it an excellent choice for use in structures that are exposed to the elements. Decks, piers, and other outdoor structures built with marine grade plywood are able to resist the damage that comes with constant water exposure, such as swelling, warping, and decay.
Furniture and Outdoor Structures
Beyond boats and docks, marine grade plywood is used for outdoor furniture and structures, especially in coastal areas. From chairs and tables to outdoor kitchens and storage sheds, marine grade plywood offers both durability and aesthetic appeal.
Outdoor furniture made from marine grade plywood can withstand exposure to sun, rain, and salty air without losing its structural integrity. Its resilience ensures that it remains functional and attractive even after years of use in harsh conditions.
Siding and Cladding
For waterfront homes or coastal buildings, marine grade plywood can be used as exterior cladding or siding. Its ability to resist water and weather damage makes it an excellent choice for buildings exposed to high humidity, salty air, and heavy rainfall.
Marine grade plywood can provide both durability and aesthetic appeal when used as siding for homes and buildings located near the ocean. Its resistance to moisture, rot, and UV radiation ensures that the structure remains protected from the elements while also looking attractive.
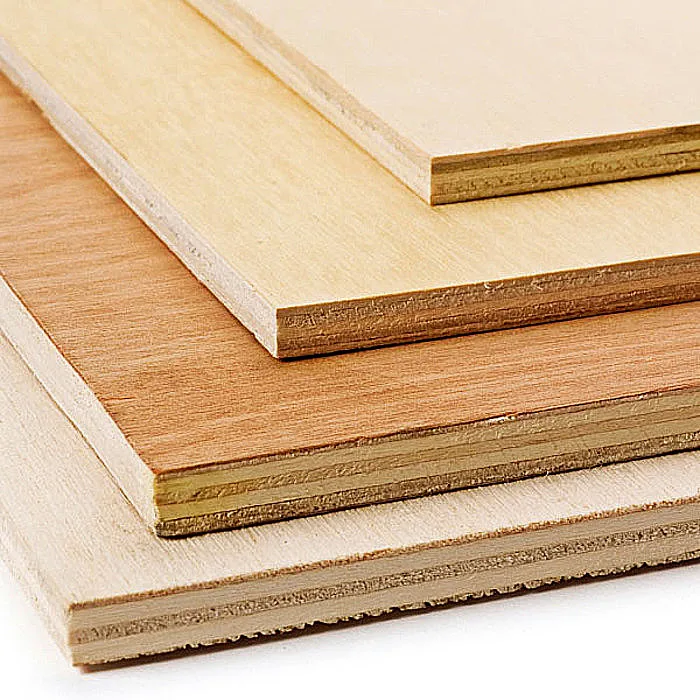
Advantages of Using Marine Grade Plywood
Superior Water Resistance
Marine grade plywood is specifically engineered to resist water and moisture. This makes it highly suitable for applications where exposure to water is constant or frequent. Whether you’re building a boat or a dock, marine grade plywood ensures your structure remains intact and functional for years to come.
The superior water resistance of marine grade plywood ensures that it doesn’t succumb to the damage caused by constant water exposure, making it ideal for marine applications where moisture is a constant challenge.
Increased Longevity
The durability of marine grade plywood ensures that it will last for many years in harsh environments. Unlike regular plywood, which may degrade quickly when exposed to moisture, marine grade plywood can withstand long-term exposure to water and weather conditions.
With proper maintenance, marine grade plywood can continue to perform well for decades, even in challenging environments where other materials would fail. Its long lifespan makes it a cost-effective choice for long-term projects.
Structural Integrity
Marine grade plywood maintains its strength even in challenging conditions. It’s able to handle physical stresses, impacts, and heavy loads, making it an ideal material for structural applications in boats, docks, and outdoor buildings.
Whether used for supporting a boat’s framework or constructing a dock, marine grade plywood maintains its structural integrity despite exposure to the rigors of marine environments.
Aesthetic Quality
The fine finish and smooth surface of marine grade plywood contribute to its use in visible applications like boat interiors and furniture. The natural beauty of the wood, combined with its durability, ensures that projects constructed with marine grade plywood look as good as they perform.
Whether you’re building a boat, constructing outdoor furniture, or creating a home by the coast, marine grade plywood can help you achieve the perfect balance of functionality and beauty.
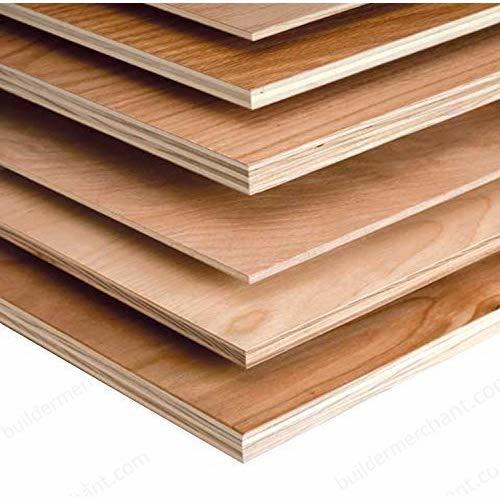
How to Choose the Right Marine Grade Plywood
Thickness Selection
When selecting marine grade plywood, thickness is an important factor to consider. Common thicknesses include 1/4″, 1/2″, and 3/4″. The right thickness will depend on the specific application and the amount of weight and stress the plywood will need to support.
Thicker plywood is necessary for load-bearing structures, while thinner plywood may be more suitable for non-structural applications like interior surfaces or paneling. It’s important to choose the right thickness for your specific needs to ensure the plywood performs optimally.
Choosing the Right Wood Type
Different wood species offer varying levels of strength, durability, and aesthetic appeal. Okoume, mahogany, and Douglas fir are popular choices, but the right wood for your project will depend on your needs, whether it’s for structural strength, visual appeal, or weight considerations.
For example, if you’re building a boat that requires lightweight yet durable plywood, okoume marine plywood might be your best choice. For applications where strength is paramount, Douglas fir marine plywood could be ideal.
Checking the Certification
Ensure that the marine grade plywood you purchase meets recognized standards, such as BS 1088 or ASTM certifications. These certifications guarantee that the plywood has been manufactured to meet the necessary quality and performance criteria.
Certification helps you ensure that the plywood you’re purchasing meets the rigorous requirements needed for use in marine environments.
Examining the Quality
Before purchasing marine grade plywood, it’s essential to inspect it for quality. Even though it meets a specific standard like BS 1088 or ASTM, not all marine plywood is created equally. When inspecting the plywood, look for any defects such as voids, knots, or visible damage to the surface. These imperfections can compromise the plywood’s strength and water resistance.
Make sure to check the bonding of the adhesive. The veneers should be tightly bonded without any gaps or visible delamination. A plywood sheet with poor adhesive bonding will not perform well in marine environments, as moisture could seep in and lead to degradation. Ensure the surface is smooth and free from any signs of damage or wear.
A thorough inspection of the plywood before purchasing helps avoid problems later. Remember, choosing high-quality marine grade plywood means ensuring the longevity and durability of your project, whether it’s a boat, dock, or any other structure exposed to water.

Installation and Maintenance of Marine Grade Plywood
Proper Installation Techniques
When installing marine grade plywood, it’s essential to use the right techniques to ensure a long-lasting, durable result. For boat construction, the plywood should be installed using waterproof fasteners that won’t rust or corrode when exposed to water. These include stainless steel screws or bolts, which are resistant to the effects of saltwater.
If the plywood is being used for docks or exterior structures, be sure to install it in a way that prevents water from pooling on the surface. Water retention can cause damage over time, leading to swelling, warping, or even rot. For boatbuilding, it’s crucial to seal the edges and seams with waterproof sealants or caulk to prevent water infiltration.
For optimal results, always follow manufacturer guidelines for installation, as different types of marine grade plywood may have slightly different requirements. Proper installation ensures that the plywood’s water-resistant qualities remain intact and that the structure remains stable and functional in harsh marine conditions.
Sealing and Protecting the Surface
To maximize the lifespan of marine grade plywood, it’s essential to protect the surface with appropriate coatings. Varnishes, marine-grade paint, or epoxy coatings are commonly used to seal the plywood and provide an extra layer of protection from water, UV rays, and physical wear.
Varnish offers a smooth, glossy finish that enhances the appearance of the plywood while providing water resistance. Marine-grade paints offer a protective barrier against moisture and UV radiation, preserving the plywood’s integrity and appearance. Epoxy coatings are often used for boat hulls or structural components that are exposed to the harshest conditions, providing a robust and durable layer of protection.
Regularly re-coating the surface with protective layers will extend the life of marine grade plywood and ensure that it continues to resist the damaging effects of water, sunlight, and physical stress.
Maintenance Tips
Maintaining marine grade plywood involves periodic checks and cleaning to ensure that it remains in good condition. Regularly inspect the plywood for any signs of damage, such as cracks, swelling, or discoloration. This is particularly important for areas exposed to continuous water exposure, such as boat hulls or dock surfaces.
When cleaning marine grade plywood, avoid harsh chemicals that could damage the surface. Instead, use gentle, non-abrasive cleaners designed for marine applications. After cleaning, inspect the plywood thoroughly to identify any issues before they become more severe.
If you find any damage, take action immediately to prevent further deterioration. For minor scratches or scuffs, lightly sand the area and apply an additional protective coating. By addressing issues early on, you can prevent more extensive damage and extend the life of your marine grade plywood.
Repairing Marine Plywood
Even with regular maintenance, damage to marine grade plywood can occur. The most common issues include cracks, chips, or delamination. If you notice minor cracks, you can often repair them by filling the gap with waterproof epoxy or wood filler. Sand the area smooth, and then reapply the protective coating.
If the plywood has delaminated or is severely damaged, you may need to replace the affected section. Delamination occurs when the layers of plywood separate due to exposure to water, and it can compromise the structural integrity of the plywood. In such cases, removing the damaged section and replacing it with new marine grade plywood is the best solution.
By following proper maintenance and repair procedures, you can ensure that marine grade plywood continues to perform at its best and withstand the harsh conditions it was designed for.
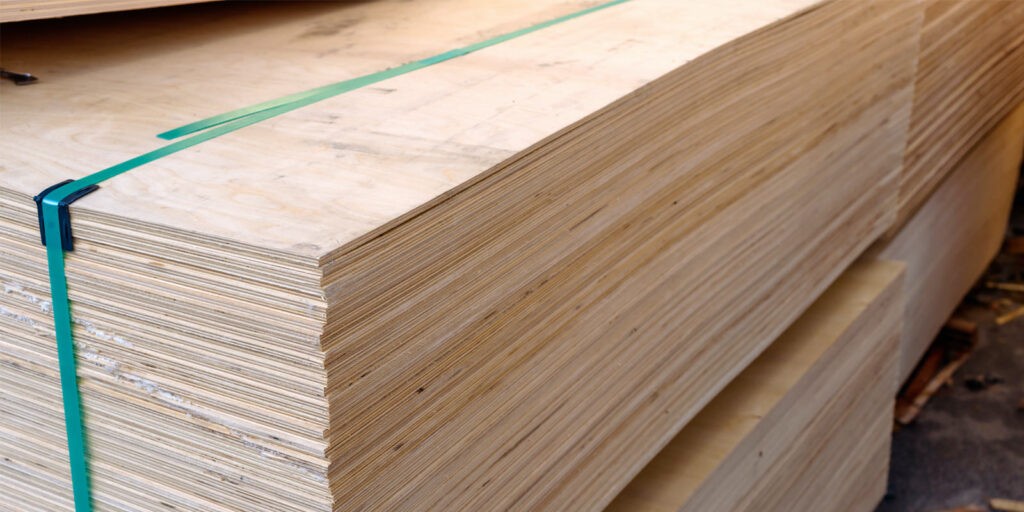
Environmental Considerations and Sustainability
Sustainable Sourcing of Marine Plywood
As concerns about environmental sustainability grow, sourcing marine grade plywood from responsibly managed forests has become increasingly important. Many manufacturers now offer marine grade plywood certified by the Forest Stewardship Council (FSC), which ensures that the plywood comes from forests that are managed in an environmentally responsible manner.
By choosing marine grade plywood with FSC certification, you can be confident that your materials are sourced in a way that supports forest conservation and sustainable land management practices. This certification helps protect ecosystems, reduce deforestation, and promote the health of forests, ensuring that future generations can continue to benefit from these valuable natural resources.
When purchasing marine grade plywood, always look for products with relevant certifications like FSC or other sustainability-focused labels. This choice supports not only the durability of your project but also the health of the planet.
Impact of Marine Plywood on Ecosystems
The production of marine grade plywood can have an impact on both forest and marine ecosystems. The extraction of timber can contribute to deforestation if not managed properly, and the manufacturing process may generate pollutants. However, with the rise of eco-conscious sourcing and production practices, many manufacturers are working to minimize these environmental impacts.
By choosing high-quality, sustainably sourced marine grade plywood, you’re helping reduce the negative impact on forests and ecosystems. Additionally, many companies are increasingly investing in more eco-friendly production methods, such as reducing waste, using low-emission adhesives, and recycling materials.
Supporting these efforts by purchasing environmentally friendly products ensures that your project — whether it’s a boat, dock, or coastal structure — doesn’t come at the expense of the environment. As demand for sustainable practices grows, the industry will continue to evolve and offer even more eco-friendly options for builders.
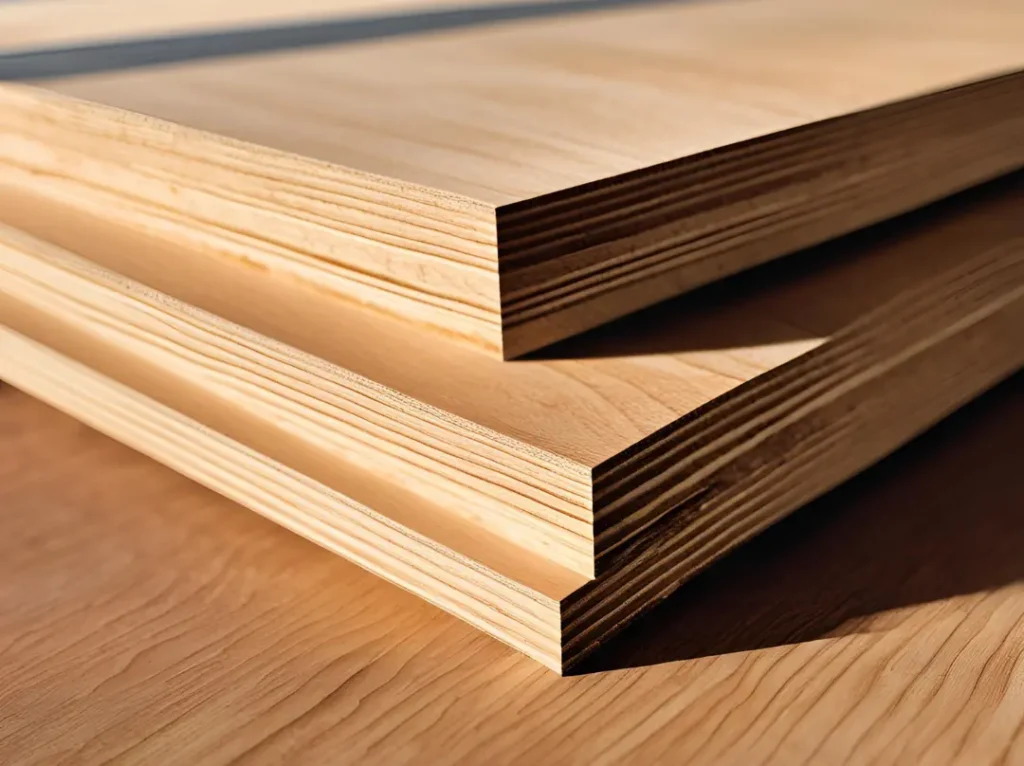
Frequently Asked Questions
Can Marine Grade Plywood be Used for Outdoor Furniture?
Yes, marine grade plywood is an excellent choice for outdoor furniture, especially in coastal areas where exposure to moisture and UV radiation is a concern. The plywood’s water resistance and durability make it ideal for creating long-lasting outdoor furniture.
In addition to its practical benefits, marine grade plywood also provides an attractive finish, making it a popular choice for creating high-quality, weather-resistant furniture for outdoor spaces.
How Long Will Marine Plywood Last in Water?
When properly installed and maintained, marine grade plywood can last for many years in water. It is specifically engineered to resist moisture, rot, and swelling, ensuring it can endure prolonged exposure to water without degrading.
The lifespan of marine grade plywood depends on various factors, including the quality of the plywood, the level of exposure to water, and how well it is maintained. With regular care and protective coatings, marine grade plywood can last up to 20-30 years or more in marine environments.
What is the Difference Between Marine Grade Plywood and Pressure-Treated Plywood?
The main difference between marine grade plywood and pressure-treated plywood lies in their construction and intended use. Marine grade plywood is made with high-quality veneers and waterproof adhesives to withstand prolonged water exposure without degrading. Pressure-treated plywood, on the other hand, is treated with chemicals to resist rot and insect damage but may not be as effective in preventing water penetration over the long term.
While both types of plywood are resistant to moisture, marine grade plywood is specifically designed for marine environments and provides superior water resistance and durability.
Can I Use Marine Plywood for Building a Dock or a Jet Ski Ramp?
Yes, marine grade plywood is perfect for building docks, jet ski ramps, and other structures exposed to constant water contact. Its resistance to moisture, rot, and physical wear makes it an ideal material for such applications. It will perform well in both freshwater and saltwater environments, ensuring a long-lasting, stable structure.
Conclusion
In summary, marine grade plywood stands out as a superior material for a wide range of applications that require strength, durability, and water resistance. From boatbuilding to dock construction, this plywood offers unmatched performance in marine environments. Its resistance to moisture, rot, and UV radiation ensures that it maintains its integrity over time, even when exposed to the harshest conditions.
Whether you’re constructing a boat, deck, or coastal home, choosing the right marine grade plywood is essential for the success of your project. Be sure to consider the type of wood, quality standards, and proper installation and maintenance techniques to get the most out of your material.
By opting for marine grade plywood, you’re investing in a material that not only performs well but also contributes to the sustainability of our ecosystems. Make sure to choose FSC-certified options whenever possible, and enjoy the durability and beauty of your finished project for many years to come.